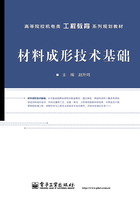
1.3铸造应力及铸件的变形与裂纹
当铸件的固态收缩受到阻碍时,在铸件内部产生的内应力称为铸造内应力。当铸造应力方向与铸件所受外力方向相同时,铸件的实际承载能力会降低。此外,铸造应力还是引起铸件产生变形和裂纹的基本原因。
1.铸造应力
按照内应力的产生原因,可分为热应力和机械应力两种。
1)热应力
热应力是由于铸件各部分冷却速度不同,以至于在同一时间内铸件各部分收缩不一致、相互约束而引起的内应力。
为了分析热应力的形成过程,首先应了解固态金属自高温冷却到室温时力学状态的变化。固态金属在再结晶温度T再(钢和铸铁的T再为620~650℃)以上处于塑性状态,此时,在较小的应力作用下,便可发生塑性变形(即永久变形),其内应力在变形后可自行消除;在再结晶温度以下呈弹性状态,此时,在应力作用下,仅能产生弹性变形,变形后应力仍然存在。
图1-5所示的是热应力形成过程及应力框的粗、细杆冷却曲线示意图。如图1-5(a)所示,应力框由长为L0的一根粗杆I和两根细杆Ⅱ及上、下横梁整铸而成,它用来分析热应力的形成过程。由该图可见,杆I与杆Ⅱ的截面厚度不同,冷却速度不一,两杆的收缩不一致,因而产生了内应力。其具体形成过程可分为如下3个阶段。

图1-5 热应力的形成
“+”表示拉应力;“-”表示压应力
(1)第1阶段(T0~T1)此时铸件处于高温阶段,两杆均处于塑性状态,尽管此时两杆的冷却速度不同,收缩也不同步,但瞬时存在的应力通过塑性变形可自行消除,在铸件内不会产生应力。
(2)第2阶段(T1~T2)进入此阶段后,冷速较快的细杆Ⅱ已进入弹性状态,而粗杆I仍处于塑性状态,此时由于细杆Ⅱ冷速快,收缩大于粗杆I,所以粗杆I受压缩,细杆Ⅱ受拉伸(如图1-5(b)所示),形成了暂时内应力,但此应力因粗杆I发生的微量受压塑性变形而自行消失(如图1-5(c)所示)。
(3)第3阶段(T2~T3)进一步冷却到更低温度,粗杆I也处于弹性状态,此时,尽管两杆长度相同,但所处的温度不同。粗杆I的温度较高,还将进行较大的收缩,细杆Ⅱ的温度较低,收缩已趋停止。因此,粗杆I的收缩必然受到细杆Ⅱ的强烈阻碍,于是,在粗杆I中产生拉应力,而细杆Ⅱ则受到杆I因收缩而施与的压应力(如图1-5(d)所示)。冷却到室温时,框中就产生了残余热应力。
由此可见,热应力使铸件冷速较慢的厚壁或心部受拉应力,冷速较快的薄壁或表层受压应力。铸件的壁厚差别越大,合金线收缩率越高,弹性模量越大,产生的热应力就越大。
2)机械应力
机械应力是合金的固态收缩受到铸型或型芯的机械阻碍而形成的内应力。如图1-6所示的轴套铸件在冷却收缩时,其轴向受砂型阻碍、径向受型芯阻碍而产生机械应力。显然,机械应力将使铸件产生拉伸或剪切应力,其大小取决于铸型及型芯的退让性,当铸件落砂后,这种应力可局部甚至全部消失。然而,若机械应力在铸型中与热应力共同起作用,则将增大铸件某部位的拉伸应力,促使铸件产生裂纹倾向。

图1-6 轴套机械应力示意图
铸造应力使铸件的精度和使用寿命都大大减小。在存放、加工和使用过程中,铸件内的残余应力将会重新分布,使铸件产生变形和裂纹。其中,机械应力虽然是一种暂时应力,但是当它和其他应力叠加时,将会增大铸件产生变形和裂纹的倾向,因此,必须加以预防或消除。预防热应力的基本途径是尽量减小铸件各个部位间的温差,使各部分收缩一致,可采用同时凝固原则。此外,改善铸型和砂芯的退让性,减小机械阻碍作用,以及通过热处理等方法也可减小或消除铸造应力。
2.铸件的变形及防止
如果铸件存在内应力,则铸件处于不稳定状态,它将自发地通过变形来减小其内应力使其趋于稳定状态。当铸造残留应力超过金属的屈服强度时,往往会产生变形。
如前所述,在热应力作用下,铸件厚的部分受拉应力,薄的部分受压应力,因此变形总是朝着冷却慢的厚的部分方向凹陷,而薄的部分发生外凸。如图1-7所示的T形梁,当板Ⅰ厚、板Ⅱ薄时,浇注后板I受拉,板Ⅱ受压,若铸件的刚度不够,将发生板I内凹、板Ⅱ外凸的变形。反之,当板I薄、板Ⅱ厚时,将发生反向翘曲。

图1-7 T形梁铸钢件变形示意图
图1-8所示的是机床的床身铸件,其导轨部分较厚,冷却较慢,受拉应力;其床壁较薄,受压应力,最后产生导轨内凹的翘曲变形。

图1-8 机床床身翘曲变形
图1-9所示的是平板铸件(如图中的双点画线所示)。虽然其厚薄均匀,但由于平板中心部位比四周冷却慢,致使中心部位受拉应力,周边受压应力,且铸型上面又比下面散热快,于是平板产生如图所示的变形。

图1-9 平板铸件的变形
变形会使铸造应力重新分布,残余应力减小,但不会完全消除。铸件变形后,常因加工余量不足而报废或铸件放不进夹具而无法加工。为了防止铸件产生变形,除在铸件设计时尽可能使铸件的壁厚均匀、形状对称外,还可以采用反变形法、时效处理等方法防止变形。反变形法是根据铸件的变形规律,在模样上预先留出相当于铸件变形量的反变形量,以抵消铸件的变形。时效处理包括自然时效和人工时效。自然时效是将铸件置于露天场地半年以
上,使其缓慢地发生变形,从而使内应力消除或减小。人工时效是将铸件加热到550~650℃进行去应力退火。时效处理宜安排在铸件粗加工之后进行,以便将粗加工所产生的内应力一并消除。
3.铸件的裂纹及防止
当铸件的内应力超过合金的强度极限时,铸件将产生裂纹。按裂纹形成的温度范围分为热裂纹和冷裂纹两种。
1)热裂纹
热裂纹是铸件在凝固后期高温下形成的。裂纹沿晶粒边界产生并扩展,其裂纹短,缝隙宽,形状曲折,裂纹周边呈氧化色。
由于热裂纹是在合金凝固后期的高温下形成的,此时金属绝大部分已成固体,但晶粒间还存在少量液体,其强度很低。例如,含碳0.3%(质量分数)的碳钢在室温的抗拉强度大于480MPa,而在1380~1410℃的抗拉强度仅为0.75MPa,这时,铸件中有较小的铸造应力,就可能引起热裂纹。尤其是当铸造合金含硫时,容易形成低熔点FeS共晶(988℃)。这些低熔点共晶呈液态薄膜状存在于晶界上,削弱了晶粒间的结合强度,在铸造应力作用下极易沿晶界产生裂纹。热裂纹在铸钢件和铝合金铸件中较常见。
热裂纹一般分布在有尖角或断面突变的应力集中部位或热节处。为防止热裂纹,铸造时应尽量选择凝固温度范围小、热裂倾向小的合金,改善铸件结构,设计合理的铸造工艺,提高型芯的退让性。此外,对于铸钢件和铸铁件,严格控制其硫含量,可显著提高金属的抗热裂能力。
2)冷裂纹
冷裂纹是铸件冷却到较低温度时形成的裂纹。裂纹细小规则,呈连续直线状,有金属光泽或轻微氧化色。
冷裂纹常出现在铸件受拉应力的部位,尤其是在应力集中的部位。脆性大、塑性差的金属,如白口铸铁、高碳钢及高锰钢等合金铸件容易产生冷裂纹,大型复杂的铸件也易形成冷裂纹。
防止冷裂纹的方法除尽量减小铸造应力外,还应控制铸造合金中的含磷量,避免生成冷脆的铁磷共晶物Fe3P。此外,设置防裂肋也可有效防止铸件裂纹。图1-10所示的是在T形铸件接头处设量的防裂肋。防裂肋的厚度一般为铸件壁厚的1/3~1/5。

图1-10 防裂肋