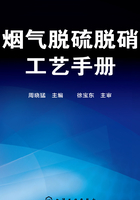
3 脱硫工艺设计
3.1 脱硫工艺
3.1.1 工艺流程
3.1.1.1 石膏湿法脱硫
典型的石灰石/石灰-石膏湿法烟气脱硫工艺流程如图3-1所示。

图3-1 典型石灰石/石灰-石膏法脱硫工艺流程
3.1.1.2 氨水湿法脱硫
典型的氨水湿法烟气脱硫工艺流程如图3-2所示。

图3-2 典型氨水湿法烟气脱硫工艺流程
3.1.2 系统描述(氨法)
3.1.2.1 系统构成
锅炉烟气经进口挡板门进入脱硫增压风机,通过烟气换热器后进入吸收塔,洗涤脱硫后的烟气经除雾器除去带出的小液滴,再通过烟囱排放。脱硫副产物经过旋流器、离心机脱水成为脱水硫酸铵。
烟气脱硫装置应能在锅炉最低稳燃负荷工况和BMCR工况之间的任何负荷持续安全运行。烟气脱硫装置的负荷变化速度应与锅炉负荷变化率相适应。
新建脱硫装置的烟气设计参数宜采用锅炉最大连续工况(BMCR)、燃用设计燃料时的烟气参数,校核值宜采用锅炉经济运行工况(ECR)、燃用最大含硫量燃料时的烟气参数。已建电厂加装烟气脱硫装置时,其设计工况和校核工况宜根据脱硫装置入口处实测烟气参数确定,并充分考虑燃料的变化趋势。烟气脱硫装置的脱硫效率一般应不小于95%,主体设备设计使用寿命不低于30年,装置的可用率应保证在95%以上。
3.1.2.2 氨水系统
吸收液制备系统可按两套或多套装置合用设置,但一般应不少于两套;当电厂只有一台机组时可只设一套。制备系统的出力应按设计工况下消耗量的150%选择,且不小于100%校核工况下的消耗量。
3.1.2.3 烟气系统
从锅炉来的热烟气经增压风机增压后,进入烟气换热器(GGH)降温侧冷却后进入吸收塔,向上流动穿过喷淋层,在此烟气被冷却到饱和温度,烟气中的SO2被循环液吸收。除去SOx及其他污染物的烟气经GGH加热至80℃以上,通过烟囱排放。
GGH是利用热烟气所带的热量,加热吸收塔出来的冷的净烟气;设计条件下没有补充热源时,可将净烟气的温度提高到80℃以上。GGH正常运行时,清洗系统每天需使用蒸汽吹灰三次;系统还配有一套在线高压水洗装置,约一个月使用一次。自动吹灰系统可保证GGH的受热面不受堵塞,保持净烟气的出口温度。
烟道上设有挡板系统,包括一台FGD进口原烟气挡板,一台FGD出口净烟气挡板和一台旁路烟气挡板。在正常运行时,FGD进口/出口挡板开启,旁路挡板关闭。在故障情况下,开启烟气旁路挡板门,关闭FGD进出口挡板,烟气通过旁路烟道绕过FGD系统直接排到烟囱。在BMCR工况下,烟道内任意位置的烟气流速不大于15m/s。
脱硫增压风机宜装设在脱硫装置进口处,其参数应按下列要求考虑。
①大容量吸收塔的脱硫增压风机宜选用静叶可调轴流式风机或高效离心风机。当风机进口烟气含尘量能满足风机要求,可采用动叶可调轴流式风机。
②300MW及以下机组每座吸收塔,宜设置一台脱硫增压风机,不设备用。对600~900MW机组,也可设置两台增压风机。
③增压风机的风量应为锅炉满负荷工况下的烟气量的110%,另加不低于10℃的温度裕量;增压风机的压头应为脱硫装置在锅炉满负荷工况下并考虑10℃温度裕量下阻力的120%。
烟气系统宜装设烟气换热器,脱硫后烟气温度一般应达到80℃以上排放。烟气换热器下部烟道应装设疏水系统。可以选择管式换热器或回转式换热器,当原烟气侧设置降温换热器有困难时,也可采用在净烟气侧装设蒸汽换热器。
烟气脱硫装置宜设置旁路烟道。旁路挡板门的开启时间应能满足脱硫装置故障不引起锅炉跳闸的要求。烟道挡板宜采用带密封风的挡板,旁路挡板门也可采用压差控制不设密封风的单挡板门。
3.1.2.4 吸收系统
吸收系统的功能是对烟气进行洗涤,脱除烟气中的SO2,同时去除部分粉尘,浓缩吸收SO2生成的硫酸铵。烟气从吸收塔中部进入,均匀分布在塔内,流速下降到4m/s以下。烟气的入口段为耐腐蚀、耐高温合金材料,进口处设工艺水喷淋降温装置,使烟气温度降到60℃左右,这是氨吸收二氧化硫反应的最佳温度。进入吸收区的烟气,在上升过程中与吸收液逆流接触,烟气中的二氧化硫被吸收液中的氨水和亚硫酸铵吸收脱除。
吸收塔底部为浆池,用来容纳硫酸铵浆液,氧化生成的亚硫酸铵、氨水也被注入浆池中。浆池的容积足够保证能够完成亚硫酸铵的氧化和氨水的中和反应,确保进入泵的硫酸铵浆液成分稳定。在喷淋的过程中,烟气进一步饱和增湿,处理后的净烟气经过除雾器,除去大部分游离水由塔顶烟囱排出。吸收塔上部布置二级内置式除雾器,整个系统压降≤1200Pa,同时设置进口烟气超温、粉尘含量过高连锁系统,以保证脱硫系统的正常运行。
吸收塔入口的布置是精心设计的,以保持朝向吸收塔有足够的向下倾斜坡度,从而保证烟气的停留时间和均匀分布,避免烟气的旋流及壁面效应。循环系统采用单元制设计,通过喷淋层保证吸收塔内200%的吸收液覆盖率。烟道侧板和底板装有工艺水冲洗系统,冲洗自动周期进行。冲洗的目的是为了避免浆液带入烟道后干燥黏结。在入口烟道装有事故冷却系统,事故冷却水由工艺水泵提供。
脱硫装置设计温度采用锅炉设计煤种BMCR工况下,从主机烟道进入脱硫装置接口处的运行烟气温度。新建机组同期建设的运行温度,一般为锅炉额定工况下,脱硫装置进口处运行烟气温度加50℃。300MW以上机组宜一炉一塔,200MW以下机组宜两炉一塔。
吸收塔宜采用钢结构,内壁采用衬胶或衬树脂鳞片或衬高镍合金板。塔外应设置供检修维护的平台和扶梯,设计荷载不应小于4000N/m2,平台宽度不小于1.2m,塔内不应设置固定式的检修平台。塔内与喷嘴相连的浆液管道应考虑检修维护措施,应考虑不小于500N/m2的检修荷载。
吸收塔应装设除雾器,除雾器出口的雾滴浓度应不大于75mg/m3(标态)。除雾器应考虑检修维护措施,支撑梁的设计荷载应不小于1000N/m2。除雾器应设置水冲洗装置。
浆液循环泵入口应装设滤网等防止固体物吸入的措施。当采用喷淋吸收塔时,吸收塔浆液循环泵宜按单元制设置;按照单元制设置时,应设仓库备用泵叶轮一套;按照母管制设置时,宜现场安装一台备用泵。
脱硫装置应设置一套事故浆池或事故浆液箱,容量宜不小于一座吸收塔最低运行液位时的浆池容量。所有储存悬浮浆液的箱罐应有防腐措施并装设搅拌装置。
3.1.2.5 氧化系统
氧化空气系统的功能是把吸收所得亚硫酸铵转化成为硫酸铵,由氧化风机和氧化喷枪组成。氧化空气入塔前设有喷水降温系统,使氧化空气达到饱和状态,可有效防止氧化喷枪口的结垢。在塔底通过氧化风机,把过量的空气鼓入脱硫塔内,把吸收液中的亚硫酸铵氧化成硫酸铵,直至有晶体析出。排放泵连续地把吸收液送到硫铵系统,通过控制排出浆液流量,维持循环浆液浓度(质量分数)在8%~25%。
烟气进入吸收塔在上升过程中,与吸收液逆流接触脱除SO2气体。吸收了SO2的吸收液落入反应池,反应池通过搅拌或扰动泵,使浆液池中的固体颗粒保持悬浮状态。氧化风机将氧化空气鼓入反应池,氧化空气被分散为细小的气泡并均布于浆液中。部分在喷淋区被氧化,其余部分的
在反应池中被氧化空气完全氧化。
氧化风机宜采用罗茨风机,也可采用离心风机。当氧化风机计算容量小于6000m3/h时,每座吸收塔应设置2台全容量或3台半容量的氧化风机;或每两座吸收塔设置3台全容量的氧化风机。当氧化风机计算容量大于6000m3/h时,宜配3台氧化风机。
3.1.2.6 硫铵系统
硫铵系统的功能是把硫酸铵结晶从浆液中分离出来。当吸收液中约有5%的固体时,吸收液开始取出回收,先经硫铵排出泵进入回收系统中的旋流器。带有结晶的过饱和硫酸铵溶液,经过旋流浓缩到含固量30%的过饱和液,溢流的饱和溶液返回脱硫塔。含固量30%的过饱和液经过离心机进一步浓缩,母液通过母液槽被母液泵输送回吸收塔。离心分离得到含水率不大于10%的硫铵粉末,通过螺旋输送机被传送到床式干燥机,经热风干燥得到含水率小于1%的硫铵,包装后储存在硫铵库中用于综合利用。
如不设置浓缩结晶塔,可将脱硫塔中的硫铵溶液浓缩到约35%,然后送往硫铵后处理工序,进行蒸发结晶和离心分离。
吸收液利用热烟气的热量蒸发水分和生成硫铵,使硫铵溶液浓度达到约20%(还含有少量氯化铵),然后用浆液输送泵将硫铵溶液送入浓缩结晶塔。
在脱硫塔前设置浓缩结晶塔,喷入来自脱硫塔生成的硫铵溶液,使硫铵溶液浓缩饱和结晶,待循环液的晶浆含固量约2%时,用浆液排出泵将浆液送入一级旋流器提浓(含固量5%~10%),再送入二级旋流器进一步提浓(含固量约30%),然后送入离心机进行分离,母液返回浓缩结晶塔。
硫铵系统可按两套或多套装置合用设置,但硫铵脱水系统应不少于两套。当电厂只有一台机组时,可只设一套硫铵脱水系统,并相应增大硫铵浆液箱容量。每套硫铵脱水系统宜设置两台硫铵脱水机,单台设备出力按设计工况下硫铵产量的75%选择,且不小于50%校核工况下的硫铵产量。