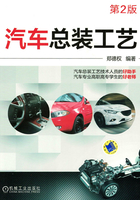
第三章 总装同步工程
第一节 同步工程介绍
一、同步工程的起源
同步工程正式起源于20世纪80年代中期,是由美国学者提出的。当时,商品市场中同类商品竞争异常激烈,制造商为了占领、保持、扩大市场的占有份额,不断推出新产品,并使其快速成为商品投放市场,在资源充足的情况下,缩短产品开发周期便成了核心问题。因此,同步工程就应运而生。
二、同步工程的定义
同步工程即SE,是英文Simultaneous Engineering的缩写,它是指对整个产品开发过程实施同步、一体化设计,促使开发者始终考虑从概念形成直到用后处置的整个产品生命周期内的所有因素(包括质量、成本、进度和用户要求)的一种系统方法。
三、同步工程的特点
同步工程的核心是将产品开发和制造生产过程中一切与其相关的工程行为组合在一起,以并行的方式统筹与实施,并将同步工程的应用哲理用于研发、生产的各个部门和领域,使工作任务既按阶段有序进行,又使各任务之间交叉有信息来往,通过信息传递,使各个部门有效沟通,将失误及时发现并改正。与传统的模式相比,同步工程具有以下几个特点:
(1)同步性 产品开发的各个子过程尽可能同步进行。
(2)约束性 将约束条件提前引入产品开发过程,尽可能满足各个方面的要求。
(3)协调性 各个子过程间密切协调以获得质量(Q)、时间(D)、成本(C)等方面的最佳匹配。
(4)一致性 产品开发过程的重大决策建立在全组成员意见一致的基础上。
四、同步工程的作用
1.降低工艺难度,减少开发成本
通过同步工程,对过于复杂的设计在保证功能和外观的前提下,经过工艺分析进行简化设计,降低工艺难度,减少工装、设备的投入,达到降低制造成本的目的。
2.修正设计缺陷,提高产品质量
通过同步工程,对设计的产品进行工艺分析,找出设计缺陷,提出改进建议或增加一定的工艺辅助设计来保证产品的生产实现,并提高设计产品本身的质量。
3.产品工装审核,促进生产实现
通过同步工程的审核把关,使工装设计满足产品设计和生产制造要求,保证其在整个产品生命周期内能够正常运转和便于维护。
4.缩短开发周期
开展同步工程工作,使工艺、制造、质量等涉及产品的部门早期介入,从各自的角度发现问题并及时解决,从而缩短产品开发周期。
五、同步工程的工作阶段
同步工程贯穿整车项目开发的全过程,根据所处阶段的不同,工作内容和输出内容有所不同。根据工作实践将同步工程主要工作定为四个阶段(品质培育阶段由制造基地负责,在此不做叙述)。
1.概念阶段
通过对整车设计目标等相关信息的分析,对整个产品总装工艺的可实现性进行论证,提供总装工艺的可行性报告。
2.模型阶段
通过对外观造型、整车主断面等相关设计输入的初步分析,发现有可能会对生产工艺产生影响的部位,并提出相应的设计变更要求。
3.工程化设计阶段
该阶段是整个产品设计思想体现的关键时期,在这个时期产生的数据决定着整个产品开发进度的快慢及产品质量的好坏。为此,该时期同步工程主要有以下三项工作:
1)对产品的生产工艺性、作业性进行分析,促使设计出来的产品既美观实用,又容易生产制造出来。
2)对生产线规划方案进行分析,使设计出来的产品符合生产线的要求,同时降低生产线的建设成本。
3)对工装开发、设备选购方案进行审核,利用现有的资源,既提高产品的生产性,同时也不降低产品的品质。
4.样车试制阶段
该阶段是对设计进行验证的时期,同时也是对同步工程工作进行验证的一个时期。所以,此时同步工程的主要工作有以下三个方面:
1)试制工艺文件准备,以正确指导试制工作的顺利进行。
2)设计变更验证,论证前期提出的设计变更是否达到要求。
3)通过对生产性、零部件状态的分析,进行相应的工艺改进,为正式生产打好基础。
同步工程已被公认为未来汽车设计、开发的必然趋势,也是我国尽快消化、吸收国外先进技术,迅速提高自主设计能力,开发自主知识产权汽车,实现由“追随模式”到“自主开发”的跨越发展的有效手段。