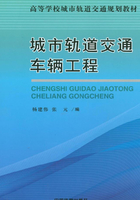
第四节 弹簧减振装置
一、概述
车辆在轨道上运行,将伴随产生复杂的振动现象。为减少有害的车辆振动,提高车辆运行的平稳性,车辆必须在走行部分安装缓和冲击和衰减振动的装置,即弹簧减振装置。车辆上采用的弹簧减振装置,按其主要作用的不同,大体可分为三类:一类是主要起缓和冲击的弹簧装置;二类是主要起衰减(消耗能量)振动的减振装置;三类是主要起定位(弹性约束)作用的定位装置,如轴箱弹性定位装置,心盘与构架之间缓冲止挡等。
铁路机车车辆通常采用的弹簧种类有:圆弹簧、板弹簧、橡胶弹簧及空气弹簧,通常采用的减振装置有:液压减振器、摩擦减振器。但在现代机车车辆上,板弹簧和摩擦减振器已经很少使用。在城轨车辆中,一系悬挂装置大多采用金属圆簧或圆锥叠层橡胶弹簧(兼作轴箱定位),保证转向架与车体之间连接,二系悬挂装置采用空气弹簧、横向油压减振器及叠层缓冲橡胶弹簧。
二、弹簧装置的作用及主要特性
(一)弹簧装置的作用及举例说明
1.弹簧装置的作用
(1)分配给各轴一定的载荷,并使所分配的重量在车轮行经不平顺线路时不致发生显著变化。
(2)缓和因线路的不平顺、轨缝、道岔、钢轨磨耗和不均匀下沉,以及因车轮擦伤、车轮不圆、轮颈偏心等原因引起车辆的振动和冲击,使运行平稳。
(3)改善机车车辆横向运动性能和曲线通过性能。
2.举例
在车轮与车体或转向架间无弹簧装置的情况下,车轮行经高度为h的不平顺处时如图3-5所示,若在车轮与车体或转向架间安装弹簧装置,则当车轮行经高度为h的不平顺处时,如图3-6所示。设轮荷重P=10000daN(1daN=10N),g为重力加速度,簧下死重量q=1900daN,弹簧刚度k=100daN/mm,线路不平顺度h=2mm,=2g,则有:
无弹簧时,车轮与钢轨间的动作用力:

有弹簧时,车轮与钢轨间的动作用力为簧下部分产生的动作用力和簧上部分对弹簧装置的反作用力kh的和,即,


图3-5 无弹簧装置时车轮行经不平顺

图3-6 有弹簧装置时车轮行经不平顺处
比较:

(二)弹簧装置的主要特性
1.主要特征
弹簧的主要特性是挠度、刚度和柔度。挠度是指弹簧在外力作用之下产生的弹性变形的大小或弹性位移量,而弹簧产生单位挠度所需的力的大小,称为该弹簧的挠度,反之单位载荷作用下产生的挠度称为该弹簧的柔度。
弹簧的特性可用弹簧挠力图表示,设纵坐标表示弹簧承受的载荷P,横坐标表示其挠度f,如图3-7所示(不考虑内部阻力的情况)。图3-7(a)表示力与挠度呈线性关系,即弹簧刚度为常量,螺旋圆弹簧的特性就是如此。图3-7(b)表示力与挠度呈分段线性关系,属于分段线性弹簧。又称准线性。图3-7(c)表示力与挠度呈曲线关系,即刚度随着载荷的变化而变化,为非线性特性。图3-7(c)中曲线1的刚度,随载荷增加而逐渐增大,如车辆上采用的一些橡胶弹簧、横向缓冲器的特性就属于这种特性。显而易见,在车辆悬挂系统中,为了减小振动,控制振动位移在一定范围内,不能使用图3-7(c)中曲线2的特性(“先硬后软”或随载荷增加,刚度逐渐变小)弹簧。

图3-7 弹簧挠力图
2.弹簧刚度与车体自振频率值的估算
在估算车体的浮沉振动的自振频率值时,要计算车辆垂向的弹簧总刚度。一般城市轨道车辆或干线铁路客车转向架均采用二系弹簧装置,即摇枕弹簧装置和轴箱弹簧装置,彼此相互串联。
设一车辆其转向架摇枕弹簧总的刚度为K∑sz,轴箱弹簧的总刚度为K∑pz,则卷弹簧刚度:

若以mi表示车体和转向架簧上部分质量之和,则车体浮沉振动的自振频率γv可由式(3-5)求得:

对于要求舒适度较高的远途客车,转向架采用弹簧的静挠度较大,车体的浮沉自振频率可低至1Hz。轻轨交通车辆,特别是地铁车辆,由于受到转向架净空和隧道轮廓的限制,或者考虑到空重车地板面高度差与站台高相配合,对空重车之间的弹簧高度差有限制,弹簧配置必定要硬些,其浮沉振动的自振频率可能要增大至1.2~2Hz。
(三)结论
由上述分析可以得出以下结论。
(1)簧下死重量g越轻,轮轨动作用力越小。因此,必须采取有效措施尽可能降低簧下重量q(而采用牵引电动机架悬式驱动装置是一种最有效地减轻簧下重量的措施)。
(2)弹簧刚度k必须选择合理。在车辆静载荷作用下的挠度称为静挠度,弹簧装置刚度小,静挠度大,使得车体自振频率低,这对车辆运行平稳性有利。所以,在条件允许的情况下,应尽可能采用较大的弹簧静挠度。
(3)为防止弹簧能量释放过程中产生共振,并限制共振振幅,必须加装液压减振器。
三、圆弹簧
(一)螺旋弹簧结构及主要参数
在铁路车辆上通常采用簧条截面为圆形的圆柱压缩螺旋弹簧,故又称圆簧,如图3-8所示。常用的弹簧材质有55Si2Mn和60Si2Mn两种。制造时还要将簧条每端约有3/4圈的长度制成斜面,使弹簧卷成后,两端成平面,以保证弹簧平稳站立,并尽量减少偏载。两端的3/4圈作为支持平面,是弹簧辅助部分,起传递载荷作用,称为弹簧支持圈。圆弹簧的特点有:(1)重量轻;(2)运动灵活;(3)无阻尼。

图3-8 圆弹簧的结构及参数
圆弹簧的主要参数有:簧条直径d,弹簧平均直径D,有效圈数n,总圈数N,一般N=n+1.5,弹簧全压缩高度Hmin,弹簧自由高度H0,弹簧指数(又称旋挠比)m=D/d,垂向静挠度fv和垂向刚度Kv等。
(二)单圈圆弹簧的特性计算
由材料力学可推导出弹簧承受的载荷P与变形(即挠度f之间的关系):
P=kvf (3-6)
说明力与挠度成正比。
这里:





稳定性校核: H0≤3.5D (3-12)
式中:G——弹簧的剪切弹性模量,一般弹簧钢G=80GPa;
Pmax——作用于弹簧上的最大垂向载荷;
α——应力修正系数,是考虑簧条的弯曲和剪切应力的非均匀分布等因素而对应力修正。其值为:

在设计车辆悬挂装置中的弹簧时,为提高车辆运行平稳性,则在结构空间位置、车钩高差等调节允许情况下,应尽量增大弹簧总静挠度。所以,设计中必须注重刚度和静挠度值的选取,为能降低刚度,增加挠度,时常在符合许用应力及有关的要求下,可以不按一般弹簧的设计要求选取某些参数值,如弹簧有效圈数的尾数值,平均直径和自由高的值,都可以不符合有关标准系列值的要求。

图3-9 双圈圆簧的结构及参数
(三)双圈圆弹簧的特性计算
有时,圆弹簧的尺寸受到安装处的位置限制或者簧条直径的限制,为利用弹簧内部空间,往往采用双圈圆弹簧,甚至三圈圆弹簧代替单圈圆弹簧,为了防止因共振而使内外圈卡死,两个圆弹簧的螺旋方向应相反,如图3-9所示。
已知单圈圆弹簧参数D、d和n,可求与之等效的双圈圆弹簧内、外圈的参数D2、d2、n2和D1、d1、n1。
在保证使内外圈簧的应力、挠度和修正系数等均与单圈时相等的条件下,双圈弹簧的特性参数如下。
1.修正系数相等,即m=m1=m2,则有:

2.应力相等,即τ=τ1=τ2,则有:

3.总载荷相等,即P=P1+P2,代入式(3-15)则有:

4.挠度相等,即f=f1=f2,则有:

5.几何关系(图3-10),即:

式中:δ为内外簧的径向间隙,一般取δ=3~5mm。
6个未知数D2、d2、n2和D1、d1、n1可由上述方程联立解出。

图3-10 几何关系示意图
四、橡胶弹性元件
(一)橡胶弹簧的特点
城市轨道车辆上采用的橡胶元件具有下列优点。
1.橡胶元件的力学性能不同于一般的金属元件,橡胶的弹性模量比金属小得多,可以获得较大的弹性变形,容易实现预想的非线性特性;
2.可以自由确定其形状,也可以根据设计要求达到在各个方向上不同刚度的要求;
3.橡胶具有较高内阻,对衰减高频振动和隔音有良好效果,且频率越高,阻尼越大,通常认为其相对阻尼系数D=0.03~0.05;
4.橡胶密度小,自重轻,维护简单,不必经常检查(不存在像金属簧那样突然折断的可能)。
由于这些特性,橡胶元件在车辆上获得越来越广泛的应用,常常用于转向架弹簧减振装置和轴箱定位装置,此外,车体与摇枕、摇枕与构架、轴箱与构架、弹簧支承面等金属件接触部位之间,常采用橡胶缓冲垫以及各种衬套、止挡等橡胶元件。因为拉伸时,橡胶对局部缺陷和表面拉伤非常敏感,橡胶弹簧一般只作压簧和扭转簧,不作拉簧。
使用最多的橡胶是天然橡胶,它具有稳定的特性,也可加些其他橡胶改善它的特性。橡胶弹簧的弹性特性不仅与其材料有关,而且还与橡胶元件的形状以及橡胶元件支承面的连接条件有关。我们通常采用块橡胶元件。橡胶与金属加钢板采用硫化或粘接的方法牢固地连接在一起,这样就提高了橡胶弹簧的可靠性和寿命。同时也增加了它的刚度和散热。
在使用橡胶弹性元件时应予以特别注意:橡胶元件的性能(弹性、强度)受温度影响较大,一般随温度升高,刚度和强度有明显的降低。同时橡胶具有蠕变的特性,即当载荷加到一定值后,虽不再增载,但变形仍在继续,而当卸去载荷后,也不能立即完全依复原状,因此橡胶弹簧的动刚度比静刚度大。另外,橡胶具有体积基本不变的特性;橡胶的耐高温、耐低温和耐油性能普遍较差,使用时间较长后容易老化。
橡胶硬度用肖氏硬度HS来表示,随温度升高而降低,如图3-11所示,硬度修正系数tE随温度变化也在图3-19中体现。图3-12是静态剪切模数GS、静弹性模数ES与HS的关系图。对于相应的动态值Gd、Ed则可根据动静刚度比(简称动静比)求得。

图3-11 橡胶弹簧硬度随温度变化的关系

图3-12 橡胶的GS、ES、d与HS的关系曲线
(二)橡胶弹簧计算
1.橡胶元件的应力计算
在简单的拉伸和压缩变形时,其应力σ与应变ε的关系式为:

式中:E为橡胶的静弹性模数;ε=δv/d(δv为橡胶弹簧的变形量,h为橡胶弹簧的厚度),该公式在拉伸应变小于20%和压缩应变小于50%这个重要的工程应用范围内有足够的精确度。
承受拉伸或压缩疲劳载荷的情况,一般应变应控制在ε<15%,此时可近似地取:
σ≈E·ε (3-20)
在剪切变形时,橡胶弹簧的剪切应力τ和剪切应变γ的关系式为:
τ=j·G·γ (3-21)
式中:G为橡胶的静弹剪模数,j为弯曲变形影响系数,τ=δi/h=tanθ,δi为剪切变形量,h是弹簧高度。试验表明,当γ<1时,τ与γ呈线性关系。
2.橡胶元件的静刚度计算
(1)承受压缩的橡胶弹簧
图3-21(a)所示为带有硫化金属扳的橡胶弹簧,当变形较小时,f/H<0.2,利用平截面假设有:

式中:F——橡胶元件的横截面积,β——由于橡胶元件两端固接引起的刚度增加系数。
对于半径为r的圆柱形橡胶弹簧,可按式(3-23)计算:


对于尺寸为a×b×H的棱柱形橡胶弹簧,刚度增加系数β应取:


棱柱形橡胶弹簧刚度计算公式为:

(2)承受剪切的橡胶弹簧
图3-13(b)所示为受剪切的橡胶弹簧,当tanγ<0.35~0.5时,力与变形成正比:

式中:f=a·b。


图3-13 橡胶弹簧承载简图
(3)承受压缩和剪切的橡胶弹簧
图3-14所示的两个对称布置并共同承载的橡胶弹簧,其垂向变形f等于压缩变形与剪切变形的几何和。

式中:α——橡胶弹簧的倾斜角。

当0<α<π/2时,采用不同的α角值,就可得到所需的刚度K和变形f。

图3-14 承受压缩和剪切的橡胶弹簧
(4)衬套式橡胶弹簧
①轴向剪切或轴向扭转的橡胶衬套
其轴向剪切刚度为:

其轴向扭转刚度为:

②承受压缩和弯曲的橡胶衬套
其径向刚度为:

其弯曲刚度为:

3.橡胶元件的动刚度计算
橡胶元件的动刚度目前主要依靠实验测定。在设计时可由式(3-35)估算:
Kd=md·Kst (3-35)
式中,Kst为静载荷作用下的橡胶元件静刚度;md为系数,表示动模数与静模数之比。
五、空气弹簧
空气弹簧就是将压缩空气密封在橡胶膜(或囊)中形成具有一定刚度的弹性体。城轨车辆转向架中广泛地采用空气弹簧作为二系悬挂装置,显著提高车辆系统的运行平稳性,大大简化转向架的结构,具有如下特点。
1.特点
(1)刚度小,当量静挠度大。空气弹簧能大幅度地增加当量静挠度,可使弹簧悬挂装置设计得很柔软,这样可降低车辆的自振频率。
(2)具有非线性特性。空气弹簧具有非线性特性,可以根据车辆振动性能的需要,设计成具有比较理想的弹性特性(曲线)。在平衡位置振动幅度较小时(即正常运行时的振动),刚度较低;若位移过大,刚度显著增加,以限制车体的振幅。
(3)刚度随载荷变化。空气弹簧的刚度随载荷变化而变化,从而可基本保持空、重车时的车体自振频率几乎相等,使空、重车不同状态的运行平稳性几乎相同。
(4)高度可调节。空气弹簧和高度控制阀并用时,可使车体在不同静载荷下,保持地板面距轨面的高度基本不变。
(5)可充分利用其横向弹性。同一空气弹簧可以同时承受三维方向的载荷。利用空气弹簧的横向弹性特性,可以代替传统转向架的摇动台装置,从而简化结构,减轻自重。
(6)能产生适宜阻尼。在空气弹簧本体与附加空气室之间设有适宜的节流孔,可以产生适宜的阻尼,以代替垂向液压减振器。
(7)具有吸振和隔音性能。空气弹簧具有良好的吸收高频振动和隔音性能。
(8)缺点:结构复杂、附件多、制造成本高、维护检修复杂。
2.空气弹簧装置系统组成
(1)系统组成
主要由空气弹簧本体、附加空气室、高度控制阀、差压阀和滤尘器等组成(图3-15)。
(2)压力空气传递过程
压力空气由列车主风管→支管→截断塞门→滤尘止回阀→空气弹簧储风缸→主管(在车底架上)→连接软管→高度控制阀→附加空气室和空气弹簧本体。
(3)高度调节阀工作原理
为了保持车体距轨面的高度不变,在车体与转向架间装有高度调节阀,调节空气弹簧橡胶囊中的压缩空气(充气、放气或保持压力),使车辆地板面不受车内乘客的多少和分布不均的影响,基本始终保持水平。
调节过程(图3-16):

图3-15 空气弹簧装置系统
1—列车主风管;2—支管;3—截断塞门;4—止回阀;5—储风缸;6—连接软管;7—高度控制阀;8—空气弹簧;9—差压阀;10—附加空气室
①在正常载荷位置,即h=H时,充气通路V→L和放气通路L→E均被关闭。
②当车体载荷增加时,此时h<H,阀动作,使V→L通路开启,压缩空气向空气弹簧充气,直至地板面上升到标定高度(即h达到H高度)为止。

图3-16 高度控制工作原理
h—地板实际高度;H—地板标定高度
③当车体载荷减小时,此时h>H,阀动作,使L→E通路开启,空气弹簧向大气排气,直至地板面下降到标定高度(即h达到H高度)为止。
(4)高度调整装置结构
不同城轨车辆所使用的高度调整装置结构有所区别,其结构如图3-17所示。该高度调整阀内使用的工作油特性如下:
种类: 硅油
黏度: 1000C.S/25℃
温度系数: 0.6
流动点: -50℃以下
高度调整阀工作过程分进气过程和排气过程,具体如图3-18和图3-19所示。

图3-17 高度调整装置结构

图3-18 载荷增加——进气过程

图3-19 载荷减少——排气过程
当然,上述调整只能在静态时进行,不能影响车体与转向架间的正常振动。那么,如何保证高度调整阀仅在静态需要调整时才起作用,而对动态振动不起作用呢?这就要求高度调整阀必须具有以下特性:
①具有不惑带(10±1)mm。
②具有时间延迟(3±1)s。
③内腔充满硅油,起阻尼作用。
(5)差动阀
每台转向架的两只气囊都通过差动阀相连,一般情况下,左右两只气囊必须保证一定的压差,可以改善列车运行状况,在曲线上运行时,可防止车体将会发生倾斜,车体左右摇摆振动时,防止加剧摇摆。如果气囊突然破裂或毁坏,差动阀将运行使转向架的两只气囊压力保持平衡。这可防止客车由于一只气囊充气、另一只气囊没有充气而向一边严重倾斜。
差压阀的结构示意如图3-20所示,当左右两侧空簧压差小于某一定值时(一般为≤0.08MPa)左右两个阀都处于关闭状态,左右两个空簧均不相通。若左边空簧压力增高,并超过该定值时,即阀中下室空气压力大于上室空气压力,左阀的弹簧受压缩,打开阀门,使压力空气从左边流向右边。

图3-20 差压阀的结构示意图
CRH2型动车组所用差动阀的型号为DP5,其设定的压力差一般为(150±20)kPa(1.5kg/cm2)。
3.空气弹簧的结构和分类
空气弹簧大体上可分为囊式和膜式2种。
(1)囊式空气弹簧
可分为单曲、双曲和多曲等形式。
特点:制造工艺简单、使用寿命长、但刚度大、振动频率高。故现代车辆上基本不用。
(2)膜式空气弹簧
分为约束膜式和自由膜式2种。
①约束膜式空气弹簧:由内、外筒将橡胶囊约束在内,如图3-21所示。
特点:刚度小、振动频率低,可方便地通过调整约束裙(内、外筒)的形状来控制其弹性特性。但橡胶囊(膜)工作状况复杂,耐久性差。

图3-21 约束膜式空气弹簧
1—外筒;2—橡胶囊;3—内筒
②自由膜式空气弹簧:无内、外约束筒,如图3-22所示。

图3-22 自由膜式空气弹簧
特点:
①无约束橡胶囊变形的内、外筒,可减轻橡胶囊的磨耗,提高使用寿命。
②安装高度低,可明显降低车辆地板面距轨面的高度。
③具有良好的负载特性,其弹簧特性可通过改变上盖板边缘的包角加以适当调整。
④重量轻。
故在现代城轨车辆上,自由膜式空气弹簧应用最广泛。
另外,空气弹簧的橡胶囊由内、外橡胶层、帘线层和成型钢丝圈组成。内层橡胶主要是用以密封,需采用气密性和耐油性较好的橡胶材质,外层橡胶除了密封外,还起保护作用。因此,外层橡胶应采用能抗太阳辐射和臭氧侵蚀并耐老化的橡胶材质,还应满足环境温度的要求,一般为氯丁橡胶。
帘线的层数为偶数,一般为两层或四层,层层帘线相交叉,并与空气囊的竖线方向成一角度布置。由于空气弹簧上的载荷主要由帘线承受,而帘线的材质对空气弹簧的耐压性和耐久性起着决定性作用,故采用高强度的人造丝、维尼龙或卡普隆作为帘线。
4.自由膜式空气弹簧刚度计算
自由膜式空气弹簧结构尺寸如图3-23所示。

图3-23 自由膜式空气弹簧结构尺寸
(1)垂向刚度k的计算



式中:p0——空气弹簧的内压力,通常轨道车辆上采用的空气压力p0<0.6MPa,一般为0.3~0.5MPa,它影响空气弹簧几何参数R的选择,静载荷P=p0A0=πR2p0。
pa——大气压力,一般计算时取pa=0.1MPa。
A0——静平衡位置时空气弹簧的有效承压面积,A0=πR2。
V0——静载荷作用下空气弹簧的容积,即V0=V1+V2,其中:V1为空气弹簧本身的容积;V2为附加空气室容积。
n——多变指数,计算时通常取n=1.3~1.38。
t、a——空气弹簧的垂向特性形状系数,取决于空气弹簧的几何形状,与其几何参数θ、φ、R有关;φ为橡胶囊圆弧部分的回转轴与空气弹簧中心线夹角,该回转轴是指圆弧中点与该弧圆心的连线;θ为橡胶囊圆弧部分形成的包角之半;R为有效承压面积么A0的半径。
(2)横向刚度k1的计算


式中: ——橡胶囊本身的横向刚度,其值需要通过实验确定;
b——空气弹簧的横向特性形状系数,取决于空气弹簧几何形状,与几何参数θ,φ,R有关。
必须注意:空气弹簧的横向刚度受到帘线角度(即帘线相对于橡胶囊的经线方向的夹角)的影响较大,通常随帘线角的增大而增加(图3-24)。橡胶囊本身的横向刚度后主要取决于帘线角的大小。设计计算时,建议值取50~100kN/m,压力高时取偏大值。

图3-24 帘线角对横向刚度的影响
六、液压减振器
(一)特征与要求
1.特征
(1)液压减振器主要是利用液体黏滞阻力所做的负功来吸收振动能量,它的优点在于它的阻力是振动速度的函数(图3-25),即:
F=q·v (3-41)

图3-25 阻尼特性曲线
其中q为阻尼系数,阻尼系数取决于节流孔的大小,节流空越大,阻尼系数越大,反之亦然;v为相对运动速度,即活塞运动速度。
(2)振幅的衰减与幅值大小有关,振幅大时衰减量也大,反之亦然。如图3-25所示。
这体现液压减振器“自动调节”减振的性能,正符合铁路车辆的需求。因而,为了改善车辆的振动性能,地铁和客车上广为采用液压减振器。
2.要求
减速器活塞工作时,工作油在油缸中流动经阻尼阀而产生减振阻力,同时,减振器将系统的振动能量转化为油液热量而逸散。对液压减振器的基本要求如下。
(1)具有合适而且稳定的阻力大小和特性;
(2)结构坚固,使用寿命长;
(3)油液物理、化学性能稳定;
(4)使用中油液不泄漏;
(5)便于维修。
(二)工作原理
液压减振器的工作原理可用图3-26来说明。活塞把油缸分成上下两个部分,摇枕振动时,活塞杆随摇枕运动,与油缸之间产生上下方向的相对位移。当活塞杆向上运动时(又称减振器为拉伸状态),油缸上部油液的压力增大,这样上下两部分油液的压差迫使上部部分油液经过心阀的节流孔流入缸下部。油液通过节流孔时产生阻力,该阻力的大小与油液的流速、节流孔的形状和孔径的大小有关。当活塞杆向下运动时(又称减振器为压缩状态)。受到活塞压力的下部油液通过心阀的节流孔流入油缸上部,也产生阻力。因此,在车辆振动时液压减振器起减振作用。

图3-26 液压减振器工作原理图
以上讨论的情况只有在活塞杆不占据油缸体积的条件下才是合适的,但实际上活塞杆具有一定的体积,当活塞上下运动时,使得油缸上部和下部体积的变化是不相等的。
设油缸直径为D,活塞杆直径为d。若活塞杆从初始位置Ⅰ向下移动距离s后达到位置Ⅱ。这样,油缸下部体积缩小πD2s/4,而上部体积增大(D2-d2)πs/4。下两部分体积之差为πd2s/4,下部排出的油液多于上部所需补充的量。为保证减振器正常工作,在油缸外增加一储油筒,在油缸底部设有进油阀,当活塞杆由Ⅰ向Ⅱ位置运动时,油缸下部油液压力增大,迫使阀瓣紧紧扣在进油阀体上,同时,多余的油液通过阀瓣中间的节沉孔流入储油筒,使减振器正常工作。反之,活塞杆向上运动,则上部因体积缩小而排出的油被量将填充不足下部因体积增大而需要的油量,所欠油量从储油筒经进油阀(阀瓣处于抬起状态)进入油缸下部,使减振器正常工作。
(三)液压减振器的结构
普通液压减振器主要由活塞、进油阀、缸端密封、上下连接、油缸、储油筒及防尘罩等部分组成,减振器内部还充有油液。
1.活塞部分是产生减振阻力的主要部分,它由活塞杆、心阀、弹簧、套阀和阀座组成,在心阀侧面下部开有直径为2mm和两个直径为5mm的节流孔。2mm直径的节流孔称初始节流孔,减振器阻力大小决定干该节流孔的大小,为了能调整阻力的大小,在心阀、阀套、阀座的底部设有0.2mm和0.5mm厚的调整垫。5mm直径的节流孔的作用是防止减振器因振动速度过大,致使油压过高,由此孔卸荷,故又称卸荷孔。在活塞上设有胀圈的主要作用是提高活塞的密封性,防止活塞磨耗后,造成过大阻力变化。

图3-27 阻尼特性调整图
液压减振器阻尼特性的调节可通过改变心阀上的节流孔的大小及弹簧预压缩量来实现(图3-27)。
(1)阀座端面加垫片——节流孔变小,阻尼增大,同时减小工作范围(图3-27的A曲线)
(2)心阀顶面加垫片——节流孔变大,阻尼减小,同时增大工作范围(图3-27的B曲线)。
(3)弹簧上部加垫片——节流孔不变,阻尼不变,但增大工作范围(图3-27的C曲线)。
2.进油阀部分装在油缸的下端,它的作用是补充或排出油液的通道,在进油阀体上装有阀瓣和锁环。
3.缸端密封部分设有比较复杂的密封结构,它一方面起着活塞杆上下运动时的导向作用,使活塞杆中心和油缸中心线保持一致,另一方面是防止油液流出和灰尘进入减振器,影响减振器的正常工作。当减振器工作时,油缸内油压最高可达25×105Pa,所以密封是一个极为重要的问题。
为了保持密封部分的性能,必须特别注意零件的各种加工精度,如同心度、垂直度和表面粗糙度等,减少零件之间的磨耗和变异。另外,在缸端上还压装一个由铸锡青铜做成的导向套。
密封圈的作用是把漏过导向套和活塞杆之间缝隙的小量油液从活塞的杆上刮下来,经过缸端盖上的回油孔回到储油筒中。密封圈的材质必须用耐寒耐油的橡胶,要求橡胶在汽油中浸泡24h后没有膨胀和油蚀现象,并要求在低温下保持一定的弹性。密封圈的刮油齿要有合理的形状和高度,齿根应防止裂纹。
4.上下连接部分它是油压减振器上下两端与转向架的摇枕和弹簧托板上的安装座相连接的部分。橡胶垫的作用:一方面可缓和上下方向的冲击;另一方面,当摇枕和弹簧托板在前后左右方向有相对偏移时,橡胶垫可有变形,减少活塞与油缸、活塞与导向套之间的偏心,使活动顺滑减小偏磨。减振器两端加装防锈帽(因经常丢失,起不到应有的作用,现已取消)后可防止雨水侵入端部,避免螺母锈蚀。
5.油压减振器,液压减振器所用的油液对减振器的性能和可靠性起着重要的作用。要求油液物理、化学性能稳定,具有防冻性,在-40℃~+40℃范围内黏度不应有很大变化,无腐蚀性等。可以使用锭子油、仪表油,变压器油以及其他专用油液。每一油压减振器内规定装油0.9dm3。
6.油压减振器的阻尼特性计算。根据理论分析和实验结果,SFK1型油压减振器的阻尼特性如下。


式中:P拉、P压——拉伸和压缩阻力单位为N;
v——活塞运动速度单位为mm/s;
f2、f3——芯阀节流和进油阀小孔面积单位为mm3。
综上所述:油压减振器的阻力取决于活塞运动速度和节流孔的大小。前者表示减振器的阻力将随振动频率和振幅的增长而增大,后者可用来调整油压减振器的阻力。
(四)圆弹簧和液压减振器共同工作时的特性
圆弹簧和液压减振器通常并联在一起共同工作,在机车车辆上通常可以将整车模型简化为车轮荷重系统来进行研究。典型的车轮荷重系统如图3-28所示。

图3-28 最简单的车轮载荷系统
圆弹簧和液压减振器的共同工作特性,是由圆弹簧的特性和液压减振器的特性合成而得。
(五)一般液压减振器与抗蛇行液压减振器的性能比较
必须注意:与一般液压减振器相比,抗蛇行液压减振器只是节流孔的结构有所不同,这就造成其节流特性发生变化,即抗蛇行液压减振器的卸荷速度v0远远小于一般液压减振器的卸前速度(图3-29和图3-30)。这样,就有可能同时满足有效抑制蛇行失稳和利于通过曲线的要求,即:

图3-29 阻力与振动速度的关系

图3-30 阻力与行程的关系
当车体相对于转向架蛇行增大时(通常对应于机车车辆在直道上高速运行时),其相对运动速度v很容易超过v0,使减振器阻尼力F=Fmax(饱和阻力),产生强大的阻尼作用。
当车辆通过曲线时(此时车辆运行速度较低),车体相对于转向架的回转速度v较小,且v<v0,此时减振器阻尼力F明显下降,在车体与转向架之间产生的阻力矩较小,使车辆容易通过曲线。
另外,抗蛇行液压减振器一定是纵向安装在车体与转向架之间,所以也常被称为纵向减振器(有人也称其为恒量阻尼减振器)。
(六)液压减振器性能试验
1.减振器的示功特性
减振器的示功特性是减振器在作规定往复运动的一个整周期中,其相对位移与阻尼力的关系曲线,如图3-31(a)所示。设阻尼器以某一行程2smax(其中smax是振幅),频率f作简谐振动,则在t时刻的位移s为:
s=smaxsin2πft (3-44)
设减振器的阻尼特性是线性的,即阻尼力与减振器活塞杆和工作缸的相对速度成正比:

式中,q是减振器的阻尼系数。
从式(3-43)和式(3-44)中消去时间参数t,得出下列示功特性表达式:

式(3-45)表明减振器的示功曲线是一个关于s和F的椭圆方程,它描述了给定位移的阻尼力大小。这个方程是假设阻尼系数为常数的条件下得到的,如果smax一定,改变v可以得到一组椭圆曲线簇,这样可以描绘F-v特性曲线,如图3-31(b)所示。

图3-31 改变速度时的阻尼特性
在铁道车辆应用中,常用示功特性作为考核减振器的依据,因为示功图所包围的面积表示减振器在一个振动周期中所吸收的阻尼功。减振器作为一种耗能元件在悬挂系统中应用,耗散于减振器中的能量转变为热量最终散失在大气中。
2.液压减振器实验台实验
电液伺服激振控制台的工作原理如图3-32所示,电液伺服作动器及电液伺服控制系统是减振器性能测试部分的核心,它们是相辅相成的,电液伺服作动器通过电液伺服控制系统控制来完成一定规律的运动,并进行减振器性能的测试。
其测试规范如下。
实验目的:检查减振器的工作是否正常,同时按设计要求调整阻尼系数q(N·s/mm)的大小。
实验设备:减振器示功图实验台,要求一端固定,另一端实现近似简谐运动,行程无级可调,一般使其做活塞运动,测量拉压过程的位移变化和载荷变化。
试验条件:温度:(20±2)℃;行程:0~20mm;激振频率:0~30Hz;位置:大致在减振器行程的中间。
试验方法:按照上述条件加振,采集数据处理时,采用第5周期到第8周期内记录的示功曲线。软件绘出曲线图—示功图,得出最大最小载荷,计算载荷不对称率、阻力系数。
不对称率:即对减振器进行拉、压时载荷的对称性,允许范围15%。
阻力系数:减振器的阻尼力和速度的比例就是阻尼系数(q),q=。
吸收功率:试件一个测试循环中所吸收功的平均值。该示功图的面积就是该液压减振器振动1周内所吸收的功。由该示功图就可以计算出其阻尼系数q来。

图3-32 减振器测试系统原理图