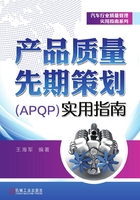
1.3 APQP的理解要点
1.3.1 APQP循环
APQP不因产品和过程的确认,项目移交生产就结束,实际意义在于质量策划的循环。一个项目经过计划、实施、研究和行动之后达产,项目达产后,转入公司日常运营各程序管理,并跟踪项目移交后的情况,对内部和外部的反馈信息分析总结,并积累经验知识,为下一个项目提供借鉴。这样就完成了一个APQP循环,并得到一定的提升,在此基础上进入下一个策划,即一个计划、实施、研究和行动循环的完成意味着进入另一个计划、实施、研究和行动,循环往复,永无止境。
图1-4所示为产品质量策划循环图。各个不同的阶段按次序排列,表示为完成各项任务的有序过程。产品质量策划循环的目的强调前期策划和实施行动。循环的计划、实施和研究为前期产品质量策划阶段;循环的行动为输出评价阶段,实施行动的重要性表现在,一是决定顾客是否满意,二是支持追求持续改进。
APQP循环是PDSA循环(戴明环)在汽车零部件新产品项目开发管理中的具体运用,产品质量策划循环表明对持续改进永无止境的追求、对顾客满意度不断的提升。

图1-4 产品质量策划循环图
1.3.2 APQP的责任范围
表1-1所示的矩阵对三种类型的组织描述了产品质量策划的功能,帮助组织确定产品质量策划的责任范围。此矩阵只是对三种基本的组织类型进行了描述,对于包含其他可能存在于组织、供应商和顾客之间有约定的质量策划关系的类型,按具体情况确定策划的责任范围。
表1-1 产品质量策划责任矩阵

对于汽车零部件制造企业,根据其所承担的项目进行分类,组织的基本类型一般分为以下三种:
1)有产品设计责任,责任范围包括产品设计和开发、过程设计和开发、生产、交付和服务。
2)无产品设计责任,只按照顾客提供的图样进行过程的设计和开发、生产、交付和服务。
3)只向顾客提供某种服务,如热处理、储存和运输等。这类组织也需要进行过程的设计和开发,并提供服务。
1.3.3 APQP防错
IATF 16949∶2016第6.1.2.2预防措施条款:“组织应确定并实施措施,以消除潜在不合格的原因,防止不合格的发生。预防措施应与潜在问题的影响程度相适应”。潜在不合格的原因是指失效尚未发生,但有可能发生的原因。事先对这些原因进行识别、分析,并采取必要措施,以预防不合格事件的发生。
预防是一种事前行为,对于识别、分析的可能失效事前采取措施预防,提高产品或过程的可靠性,使产品和过程在最容易和最低成本的情况下进行生产和运行,更大程度地降低后期更改风险,及时为顾客提供更优质的产品。
APQP整个过程贯穿着预防错误的思想,随着APQP进程推进,项目的任何工作任务都必须考虑潜在的失效与风险,采取必要的预防措施和方法,将风险降至最低。图1-5所示为APQP防错示意图。
1.3.4 APQP的时机
汽车零部件企业有下列两种情况可使用APQP:
1)新产品开发时。
2)有设计变更或制造过程变更时。

图1-5 APQP防错示意图
1.3.5 APQP的输入与输出
输入是一个过程活动所需要的信息和实物等依据,如文件、标准、材料、3D数据和计划等。输出是一个过程活动的结果,如工程图样、产品、文件和服务等。
APQP手册描述有49项输入和输出,但每一项输入和输出都是建议性的,并无强制要求。
1)APQP的输入和输出根据项目产品、过程和顾客要求和期望,其适用性是不同的,可进行删减。
2)针对质量体系标准IATF 16949中的要求,必须输入或输出。
3)APQP的输入和输出,不限于APQP手册描述的输入和输出,根据具体项目特点和顾客的要求,其输入和输出会有差别,可扩充或删减。
4)APQP的输入和输出之间并不必须是一一对应的关系,一项输入可以有几项输出,几项输入可只有一项输出。
5)当APQP实施时,尽管APQP的输入和输出是建议性的,但APQP的实施步骤必须遵循。